THIẾT KẾ QUY TRÌNH CÔNG NGHỆ GIA CÔNG CHI TIẾT CẦN LẮC MÁY BÀO
NỘI DUNG ĐỒ ÁN
Thiết kế quá trình công nghệ gia công chi tiết: CẦN LẮC
Trong điều kiện:
- Dạng sản xuất hàng loạt vừa.
- Trang thiết bị tự chọn.
Với các yêu cầu sau:
- PHẦN BẢN VẼ:
- Bản vẽ chi tiết gia công khổ giấy A0.
- Bản vẽ chi tiết lồng phôi khổ giấy A0.
- Bản vẽ sơ đồ nguyên lý khổ giấy A0.
- 02 bản vẽ kết cấu nguyên công khổ giấy A0.
- 02 bản vẽ đồ gá khổ giấy A0 .
- PHẦN THUYẾT MINH:
- Phân tích chi tiết gia công
- Chọn phôi, phương pháp chế tạo phôi và xác định lượng dư gia công.
- Lập bảng quy trình công nghệ gia công cơ
- Biện luận qui trình công nghệ.
- Thiết kế đồ gá.
- Kết luận về quá trình công nghệ
Ngày giao đề ……………, ngày hoàn thành ……………
Phần 1 : PHÂN TÍCH SẢN PHẨM
1.1.Phân tích chức năng và điều kiện làm việc của chi tiết.
1.1.1.Chức năng.
Cần lắc là một chi tiết trong máy bào.Cần lắc thuộc dạng càng .Vì càng là một chi tiết thường có một hoặc một số lỗ cơ bản cần được gia công chính xác.Các lỗ này có quan hẹ vuông góc với mặt phẳng nao đó, có quan hệ về độ song song giữa các đướng tâm lỗ . Chi tiết dạng càng thường có chức năng là cầu nối giữa chi tiết này với chi tiết khác.
Cần lắc thuộc dạng càng,làm việc chủ yếu ở rảnh 75+0.05 mm và ở 2 lỗ Ø38+0.025 và Ø32+0.025 . Ngoài ra còn có các lỗ ren M8, 3 lỗ ren M10 sâu 10, lỗ Ø6 và rãnh 40.
Cần lắc có tác dụng như 1 thanh truyền,biến chuyển động quay của máy thành chuyển động tịnh tiến của đầu dao bào.
1.1.2.Điều kiện làm việc.
Cần lắc làm việc trong môi trường thường xuyên tiếp xúc với dầu mỡ và các chất bôi trơn khác.Trong quá trình làm việc sẽ sinh ra ma lực va đập tác dụng lên cần lắc thông qua đầu dao bào.
1.2.Phân tích vật liệu chế tạo chi tiết.
Vật liệu chế tạo cần lắc là GX 18-36 .Là loại vật liệu thường được sử dụng trong việc chế tạo các chi tiết máy trong máy công cụ.
Giải thích kí hiệu:
- GX: Là kí hiệu của gang xám
- 18: Chỉ số giới hạn bền kéo .....................................................................
Phần 2 : CHỌN PHÔI,PHƯƠNG PHÁP CHẾ TẠO PHÔI VÀ XÁC ĐỊNH LƯỢNG DƯ GIA CÔNG.
2.1.Chọn vật liệu phôi.
- Vật liệu chế tạo chi tiết là gang xám GX 18-36.
- Dạng sản xuất hang loạt vừa.
- Hình dáng hình học của chi tiết khá phức tap.
→Do đó ta chọn phôi đúc ,vật liệu GX 18-36.
2.2.Phương pháp chế tạo phôi.
Để chọn phương pháp chế tạo phôi ta dựa vào các yếu tố sau:
- Hình dạng kích thước của chi tiết máy.
- Sản lượng hoặc dạng sản xuất.
- Điều kiện sản xuất của xí nghiệp.
2.21.Đúc trong khuôn cát.
- Làm khuôn bằng tay : áp dụng cho việc đúc với dạng sản xuất đơn chiếc hay những chi tiết có kích thước lớn .độ chính xác và năng xuất phụ thuộc vào tay nghề đúc.
- Làm khuôn bằng máy:áp dụng cho đúc hàng loạt vừa và hàng khối, năng xuất và độ chính xác cao.
2.22.Đúc trong khuôn kim loại.
Sản phẩm đúc có có kích thước chính xác, cơ tính cao. Phương pháp này sản xuất cho hàng loạt lớn và hàng khối. Vật đúc có khối lượng nhỏ khoảng 12 kg, hình dạng vật đúc không phức tạp và không có thành mỏng.
2.23.Đúc ly tâm.
Áp dụng vật đúc tròn xoay, do có lực ly tâm khi rót kim loại lỏng và khuôn quay, kết cấu của vật thể chặt chẻ hơn nhưng không đồng đều từ ngoài vào trong.
2.24.Đúc áp lực.
Áp dụng với các chi tiết có hình dạng phức tạp, phương pháp này cho ta độ chính xác cao, cơ tính tốt. Phương pháp đúc ly tâm và các phương pháp khác có những nhược điểm mà phương pháp đúc áp lực có thể khắc phục được. Do đó thường áp dụng cho dạng sản xuất hàng loạt lớn và hàng loạt khối, và áp dụng đối với các chi tiết nhỏ.
→ Tham khảo qua một số phương pháp đúc như trên, căn cứ vào chi tiết dạng càng, có hình dáng tương đối phức tạp, kích thước lớn và là dạng sản xuất hàng vừa.Vì thế ta chọn phương pháp đúc trong khuôn cát, mẫu kim loại, làm khuôn bằng máy, vật đúc đạt cấp chính xác II.........................
Phần 3 : LẬP BẢNG QUY TRÌNH CÔNG NGHỆ GIA CÔNG CƠ.
3.1.Xác định đường lối sản xuất công nghệ.
Trong dạng sản xuất hàng loạt vừa , QTCN được xác định theo phương pháp phân tán hoặc tập trung nguyên công,Theo nguyên tắc phân tán nguyên công thì QTCN được chia thành các nguyên côn đơn giản có thời gian như nhau.
Ở đây mỗi máy thực hiện một nguyên công nhất định,đồ gá sử dụng là đồ gá chuyên dùng .
3.2.Chọn phương pháp gia công.
Đối với dạng sản xuất hàng loạt vừa và hang loạt lớn ,nếu muốn chuyên môn hóa cao , để có năng xuất cao trong điều kiên sản xuất ở Việt Nam thì đường lối công nghệ thích hợp nhất là phân tán nguyên công.Ở đây dùng máy vạn năng,và sử dụng đồ gá chuyên dùng.
3.3.Chọn chuẩn công nghệ.
- Chuẩn công nghệ là bề mặt chi tiết được dùng để định vị chi tiết trong quá trình gia công,lắp ráp,sửa chữa.Việc chọn chuẩn công nghệ thích hợp tạo điều kiện thuận lợi cho việc thực hiện các nguyên côngđược dễ dàng ,nhanh chóng,chính xác và đảm bảo yêu cầu kỹ thuật ,chỉ tiêu kinh tế.
- Xác định chuẩn thô : là chuẩn định vị chưa gia công trên bề mặt cắt gọt,việc chọn chuẩn thô phải đảm bảo phân bố đủ lượng dư cho bề mặt gia công,và đảm bảo độ chính xác cần thiết về vị trí tương quan giữa các bề mặt với nhau,chọn chuẩn thô phải tuân thủ 5 nguyên tắc chọn chuẩn thô.
- Xác định chuẩn tinh : là chuẩn xác định trên bề mặt đã qua gia công cắt gọt.Việc chọn chuẩn tinh phải tuân thủ 5 nguyên tắc chọn chuẩn tinh.
3.4.Lập tiến trình công nghệ.
- Nguyên công I: Làm sạch phôi.
Kiểm tra phôi .
Ủ phôi.
- Nguyên công II: Phay thô mặt A .
- Nguyên công III: Phay mặt B .
- Nguyên công IV: Phay tinh mặt A .
- Nguyên công V: Khoét doa Ø38+0.025 .
- Nguyên công VI: Khoét doa Ø32+0.025 .
- Nguyen công VII: Phay thô mặt bên đầu tiên rãnh 75+0.05 .
- Nguyên công VIII: Phay thô mặt bên còn lại rãnh 75+0.05 .
- Nguyên công IX: Phay tinh mặt bên đầu tiên rãnh 75+0.05 .
- Nguyên công X: Phay tinh mặt bên còn lại rãnh 75+0.05 ..
- Nguyên công XI: Phay 2 mặt G,H .
- Nguyên công XII: Phay 2 mặt C,F .
- Nguyên công XIII: Phay 2 mặt D,E .
- Nguyên công XIV: Khoan,ta rô 3 lỗ M10 sâu 10 .
- Nguyên công XV: Khoan,ta rô M8 ,khoét lỗ bậc Þ12 sâu 5 .
- Nguyên công XVI: Khoan lỗ Þ6 .
-Nguyên công XVII: Cào rà 2 mặt bên rãnh 75+0.05 .
- Nguyên công XVIII: Tổng kiểm tra ........................................................................................................................
5.4.Tính toán sai số.
5.4.1.Tính sai số chuẩn.
Sai số chuẩn ec xuất hiện trong quá trình định vị phôi trên đồ gá và có giá trị bằng khoảng giao động kích thước từ chuẩn đo tới mặt chốt tỳ theo phương kích thước gia công ( trong phần lớn trường hợp được lấy bằng dung sai của kích thước này )
Ở đây do gốc kích thước trùng với chuẩn định vị nên sai số chuẩn bằng 0.
5.4.2.Sai số kẹp chặt.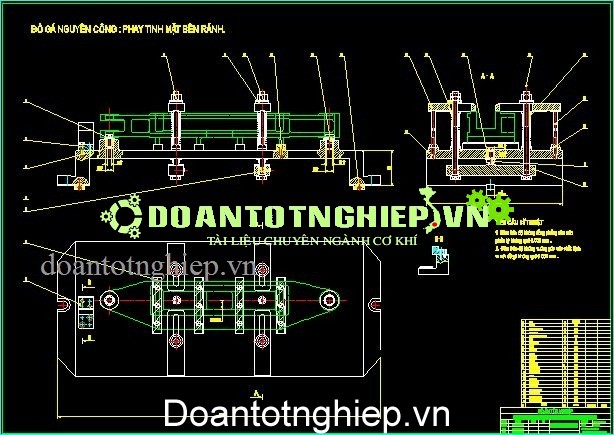
Là sai số do lực kẹp gây ra vì phương của lực kẹp vuông góc với phương của kích thước gia công nên nó không ảnh hưởng đến độ chính xác của bề mặt gia công, do đó nên sai số kẹp chặt ek =0.
5.4.3.Sai số mòn.
Trong quá trình tháo lắp chi tiết nhiều lần bề mặt chi tiết định vị bị mòn do đó phát sinh sai số mòn
Mục lục
Trang
Phần 1: PHÂN TÍCH SẢN PHẨM. 5
1.1.Phân tích chức năng và điều kiện làm việc của chi tiết. 5
1.2.Phân tích vật liệu chế tạo chi tiết. 5
1.3. Phân tích về độ chính xác gia công. 6
1.4. Xác định dạng sản xuất . 13
Phần 2: CHỌN PHÔI ,PHƯƠNG PHÁP CHẾ TẠO PHÔI
VÀ XÁC ĐỊNH LƯỢNG DƯ GIA CÔNG. 18
2.1.Chọn vật liệu phôi. 18
2.2.Phương pháp chế tạo phôi. 18
2.3.Xác định lượng dư. 19
2.4.Tính lượng dư. 21
2.5.Hệ số sử dụng vật liệu. 23
Phần 3: LẬP BẢNG QUY TRÌNH CÔNG NGHỆ GIA CÔNG CƠ . 25
3.1.Xác định đường lối sản xuất công nghệ. 25
3.2.Chọn phương pháp gia công. 25
3.3.Chọn chuẩn công nghệ. 25
3.4.Lập tiến trình công nghệ. 25
Phần 4 : BIỆN LUẬN QUY TRINH CÔNG NGHỆ. 27
Phần 5 : THIẾT KẾ ĐỒ GÁ. 106
Phần 6 : KẾT LUẬN VỀ QUÁ TRÌNH CÔNG NGHỆ. 111
Tài liệu tham khảo. 112
.
THIẾT KẾ QUY TRÌNH CÔNG NGHỆ GIA CÔNG CHI TIẾT CẦN LẮC MÁY BÀO, đồ án môn học công nghệ chế tạo máy, bài tập lớn công nghệ chế tạo máy, thiết kế quy trình công nghệ gia công chi tiết